
Continuing with the Ichabod eyepiece, I seal the outside with Bondo™ auto body putty so that the mold material won't leak in between the individual pieces of acrylic.
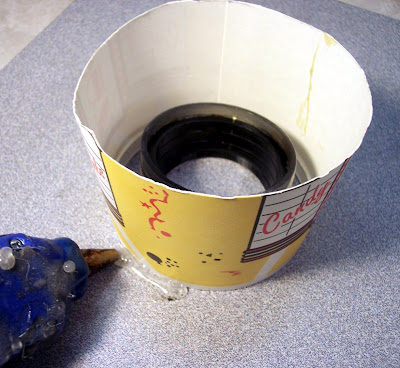
I hot glue the model to a small piece of Formica. Here I am hot gluing a paper popcorn cup down around the model to contain the rubber.

This is the model, cup and wooden dowel (
to make it easier to demold and to save on rubber) ready for the silicone rubber.

The silicone rubber RTV (
room temperature vulcanization) is ladled out with a spatula.

First I weigh out the white rubber base......

.....then I weigh out the dark blue activator, which is 10% of the base weight.

After mixing it completely with the spatula, the silicone mix is placed into a vacuum chamber to boil out any excess air. This picture shows the rubber mix boiling away (
at room temperature).

Once it is vacuumed (
deaired) the silicone rubber is poured over the model.

The next morning I demold the eyepiece, and cast it in a charcoal colored urethane resin. I sand smooth both the interior and the exterior of the casting.

Now for the decoration. Rather than add screws or bolts as I have with earlier steampunk eyepieces I have decided to add a design in bas relief. First I draw out the design with a black Sharpie™ on white paper, then scan it. Bringing it into
CorelDraw™ I vectorize it and clean up the lines, then laser cut it out of green card stock to check the fit onto the eyepiece.

All looks well so I proceed to laser cut a thin piece of foam with mirror images of my design. The pressure sensitive tape on the back allows them to be attached and ready to mold.
No comments:
Post a Comment